Smaller,
Smarter and Sustainable: Trends that Will Define the
Future of Medical Device Design
There’s never been a bigger moment for
innovation in the healthcare industry than right now.
Leading medical device manufacturers are in a race to
develop new devices that are smarter, minimally invasive
and capable of delivering better patient outcomes. But
without a trusted polymers partner to offer the materials
knowledge and testing capabilities necessary to give your
device the performance characteristics it needs — your
innovation may not be realized.
Trend 1: MINIMALLY
INVASIVE DEVICES
Patient comfort is one of the highest considerations when
developing a medical device. Manufacturers are constantly
striving to make their devices less invasive. The first
thing that comes to mind when we think of “minimally
invasive” is size. Because these types of devices are
introduced into the patient’s body through incisions that
need to be kept small, device designers know it is
critical for them to have the thinnest possible walls to
allow the largest possible delivery channel without
compromising on outer diameter (gauge).
Thin walls require materials with the appropriate physical
properties that provide a combination of strength, kink
resistance, friction reduction and extrusion
processability. Thermoplastic polyurethanes (TPUs) are a
widely used material due to the strength they impart in
minimally invasive devices, allowing manufacturers to
bring designs for optimal patient outcomes to life.
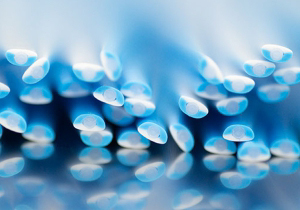
Trend 2: DEVICES WITH SMART TECHNOLOGY
An emerging trend in medical device design is utilizing
new technology to make devices smarter. For example, by
incorporating additional sensors into a catheter, you are
also able to measure flow, pressure and other factors
during an examination that help physicians to optimize the
treatment for a better patient outcome.
Another example of smarter devices are wearables such as
continuous glucose monitors (CGMs). Just as important as
the sensors that are pushed through the skin to measure
glucose levels in the body are the membranes that coat
them. CGM sensor coatings are a unique part of the
function of the device itself and are coated for multiple
reasons including: •
Immobilization of glucose-related enzymes, which fuel the
generation of electrochemical signals to the sensor.
• Exclusion of other dissolved substances that can
interfere with sensor readings and reduce device
sensitivity.
• Creation of a biocompatible interface within the body,
including prevention of sensor fouling.
Materials suppliers can evaluate how best to incorporate
and apply polymers as a coating. Suppliers can also modify
existing polymers to develop these necessary membranes and
provide critical protection to the device and to the
patient.
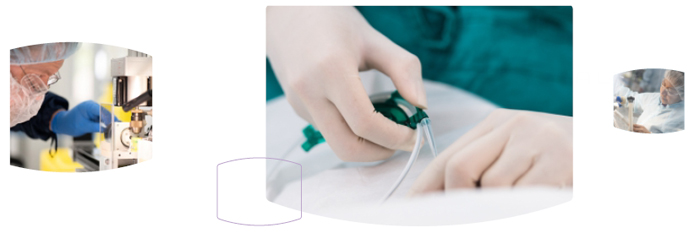
Trend 3: DEVICES MADE WITH SUSTAINABILITY IN MIND
As the healthcare industry evolves, manufacturers are
facing pressure from key stakeholders to produce devices
that use environmentally sustainable materials, implement
processes that reduce their carbon footprint, and produce
more high-quality devices that are capable of lasting
longer periods of time and meet evolving regulatory
requirements. Partnering with a materials supplier who
utilizes bio-sourced raw materials and optimized
processing techniques is key to developing more
sustainable devices. HOW
LUBRIZOL LIFE SCIENCE SUPPORTS INNOVATION IN MEDICAL
DEVICE DESIGN Device
manufacturers looking to stay ahead of the curve and
develop the next generation of medical devices will need
to innovate in terms of size, smart technology and
sustainability. Selecting the right materials and the
right partner will enable them to do so.
At Lubrizol, we are experts in the relationship between
the structure, processing, and performance of medicalgrade
TPUs. Our team designs new TPUs to achieve specific
mechanical properties that will allow medical device
designers to create smarter and smaller devices, thereby
making them less invasive, safer, and ultimately, more
effective. We also strive to
create a more sustainable environment and reduce our
carbon footprint by recycling materials and exploring
reclaiming our Isoplast® ETPU during dental aligner
manufacturing and reusing it in industrial applications.
We are also considering utilization of sustainably
bio-sourced raw materials. Furthermore, we help our
customers develop more sustainable and more reliable
medical devices, particularly in implant applications by
producing high quality materials for long term
applications. DELIVERING
VALUE BEYOND THE DEVICE To
develop an innovative device, manufacturers must think
holistically. It’s important to consider a variety of
factors including material selection, compatibility with
other materials and equipment used during procedures,
manufacturability, and how the device will be assembled,
packaged, and sterilized. At Lubrizol, we consider all
phases – from concept to commercialization to ensure the
device can deliver the required clinical performance and
desired patient outcome – it’s how we deliver value beyond
the device.
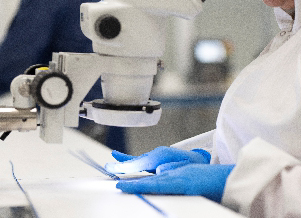
To learn more about how Lubrizol can bring your innovation
to life, visit us at go.lubrizol. com/BYDBrief or contact
Rajnish.Singh@Lubrizol.com
for more information.. |