Selection
Criteria And Critical Factors
One of the
most challenging tasks for a Medical Device Manufacturer
is selecting the right package for the Medical Device.
Device manufacturers need to look for cost-effective
packaging solutions which not only make the product
presentable but also serve their intended purpose. The
right package will have an impact in infection control,
patient safety and of course the costs of the Device
Manufacturer.
Important
points when choosing an appropriate packaging for the
Medical Device:
-
Permit Sterilization of the
Medical Device.
-
Maintain Sterility of the
Package until the package is opened.
-
Permit Aseptic removal of the
Device when presenting.
-
Protect the Device
-
Adequate protection against
microorganisms, dust, moisture etc.
-
Must be presentable.
-
Costs.
Selection Criteria
A variety
of choices in the form of Wraps, Pouches and Rigid
Containers are available for packaging Medical Devices.
We shall
restrict our discussion to Pouches as Wraps and Rigid
Containers are more specific to Hospitals than to Device
Manufacturers.
Medical
Packaging / Sterilization Packaging Products are
classified as a Class I, Non-Invasive Non-Sterile Medical
Device in the EN Standards but the US FDA classifies the
same as a Class II Medical Device which require a 510 (k)
approval.
Device
Manufacturers need to follow the following steps when
choosing a Packaging:
-
Nature of Medical Device.
(weight, dimension, sharp / protruding edges, criticality
of the device).
-
Primary, Secondary and
Tertiary Packaging (For storage and transportation).
-
Method of Sterilization
(Steam, EO, Gamma, Gas Plasma).
-
Quality Standards maintained
by the Packaging Manufacturer.
-
In-house ability to pack the
medical device (Sealing machines, clean room, qualified
staff etc.)
Material
Selection
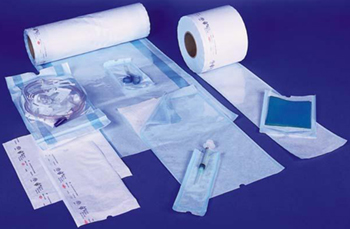
-
Disposable Peel-Open Pouches
are the most common packaging solution for Device
Manufacturers.
-
Peel-Open Pouches are
generally available in Paper/Poly combination or Tyvek/Poly
Combination.
-
Paper pouches are sufficient
for small and light-weight devices which do not have any
sharp edges.
-
Paper Pouches for device
manufacturers are generally made of a 60 / 70 gsm Medical
Grade Paper conforming to EN 868 Part 6 for EO / Gamma
Sterilization. The paper is sealed on to a transparent
laminate which make the product visible.
-
The Films should be laminated
to eliminate possibility of pin-holes, should be made from
virgin materials, should be sealable and peelable to the
paper / Tyvek, should withstand the process of
sterilization. The films are preferably transparent and
can be tinted blue / green / pink not only to make the
package more presentable but also to check the seals along
the edges clearly.
-
The Pouches are sealed on the
3-sides with a “chevron” seal on top and the bottom side
is sealed after insertion of the device in the pouch by
the manufacturer by a heat-sealing machine with a minimum
seal width of 6mm.
-
The recommended Shelf-life
post sterilization is 3 to 5 years depending on method of
sterilization, storage conditions etc.
-
Tyvek is recommended for
devices which are heavy and also which have sharp edges or
corners.
-
Tyvek pouches are generally
three times more expensive than paper pouches and need not
be used just because the product is being exported!
-
Header Bags are recommended
for Packing of tubing sets, drape, gowns and dressing
kits.
|
Emerging
Global Trends
Medical
Packaging is an evolving industry. The past few years have
seen a tremendous growth especially in India. Device
Manufacturers have moved from transparent /
opaque LDPE bags to Medical Grade Pouches.
The emerging
trends point to innovating more cost effective substrates
and films.
-
All-Over Laminated Papers,
Grid Lacquered Papers, Reinforced Coated Papers suitable
for Steam, EO & Gamma
-
Puncture and abrasion
resistant packaging for sharp instruments
-
Non-Woven Pouches
-
Header Bags with Built-in
Pouch for instruction manuals
-
Effective Sealing Technologies
-
Recyclable Plastics
Requirements For Design Of Material
Medical Grade
Peel-Open Pouches should have the following
characteristics:
-
Should be sealed correctly on
all sides
-
Peel-Strength and
seal-strength should be adequate
-
A minimum seal-width of 8mm is
recommended
-
Minimum or No Fiber Tear when
peeling open the pouch
-
Must have a “chevron” seal on
the topend and preferably a “thumb-cut” for easy gripping
and opening of the pouch.
-
Should have sufficient barrier
properties for protecting the contents
-
Should be aesthetic and
presentable
Implications Of Material Selection On Design And Packaging
Machinery
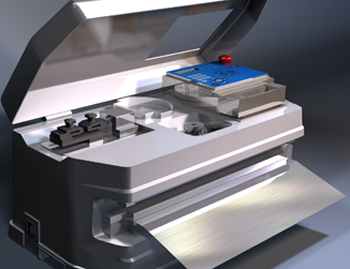
Device
Manufacturers can be classified into two broad categories:
-
Device Manufacturers with
in-house online packaging facility like Blister Packing
Machines and Device Manufactures who manually pack
devices.
-
In-puts for blister pack
machines are recommended by the machine suppliers
themselves and generally consist of pouches made of
gridlacquered paper and soft-PVC blister films.
-
Device Manufacturers who pack
devices manually procure the preformed pouches from
converters.
-
The Converters and device
manufactures mutually decide on the best possible options
in packaging. The device manufactures need to install only
a good and effective sealing machine which needs to be
validated at regular intervals.
-
Sealing quality should be
checked every day with the help sealing check strips.
-
The contents of the pouch
should occupy not more than 75% of the volume of the
pouch. Stuffing the pouch excessively will strain the
seals which may lead to the pouch opening at the time of
sterilization.
Reducing
The Cost Of Packaging Without Compromising The Quality
-
Device manufactures should
strive to achieve a right balance between costs and
quality in packaging.
-
A reduction in price need not
result in reduction in quality and vice-versa.
-
As the market for medical
pouches is growing in India, it is natural that there will
be newer entrants / converters in the market, who will
push down the prices due to competition.
-
The prices of sterilization
packaging products have reduced by all most 25% in the
past 5-6 years.
-
Competition, cheaper access to
raw materials due to bulk purchases, better machine
technology, economies of scale are some of the factors
that have led to more competitive pricing from converters.
-
Converters are offering more
customized solutions to Device Manufacturers which help in
reducing costs rather than just offer off-the-shelf
products.
-
Pre-Printed pouches with
built-in sterilization indicators are very common and help
reduce overheads of device manufactures.
Services
Offered
-
We manufacture and supply
Sterilization Packaging Products in the Form of Reels and
Pouches.
-
Generally hospitals purchase
reels and device manufactures prefer pre-formed pouches
-
Our products are compatible
with Steam / EO / Gamma Sterilization / Plasma
Sterilization processes.
-
Our products are CE Certified
and our manufacturing facility is ISO 13485 Compliant.
|