Designing And Manufacturing Of Molds For
Medical Components
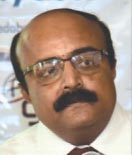
Mr. Ketan
Panchal, Production Manager,
Indo German
Tool Room, Ahmedabad. |
The best output is based on optimum inputs. Normally we
believe that the mold makers has main role to produce the best components.
The mold maker’s selection is based on low cost and minimum delivery time.
Sometime we also choose mold maker based on only quality of product. In fact
in all the case our output is samples to produce molds. Some time we also
demand merging of different features of different samples and make one
product design. Sometime we provide samples of existing mold and ask for
modification. Now all the mold makers are used to with this situation and do
the work.
The better output need more attention in the area of
product applications, standards, plastic material selection, product design
considerations, injection molding machine to be use etc,. There are
stated requirement, non stated requirement and hidden requirement.
Stated requirements are dimensions, tolerances, weight,
surface finish, fitments, applications and mold life. These are the most
important requirement which is always stated in the drawing. We should study
all the points and try to make very informative product design. |
Non stated requirements are flash free, sink mark free, warpage free etc. These
are not stated but it should be taken care as stated requirement by the mold
maker.
Hidden requirements are assembly of parts in automatic machine, automatic
packaging, adhesive use in assembly, use of temperature in post process,
sterilization, ultrasonic welding etc. These requirements should be clear in the
beginning in product design. This will clear product design requirements in the
beginning.
The above requirements are input which give better output in mold making.
Product design features
1) Parts with thick wall thickness and thin wall thickness
The plastics material is having range of minimum and maximum wall thickness.
During product design the range of plastic material thickness should be taken
care to produce defect free component.
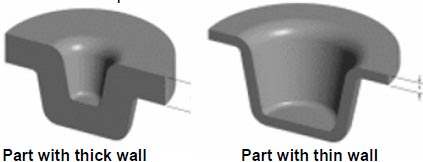
2) Parts with uniform and non uniform wall thickness
The uniform wall thickness will give warpage free component due to even cooling
of wall thickness. Some time non uniform wall thickness is the requirement of
product need better cooling to avoid warpage. More cooling is required in thick
wall area and less cooling is requiring in thin wall area. This can be judge
with mold flow analysis.
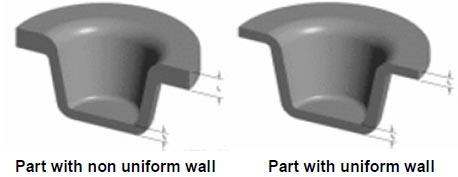
3) Sharp corners and corners with radius.
The sharp corners are not advisable in plastic products. Some radius must be
providing in the product design which make deformation free product.
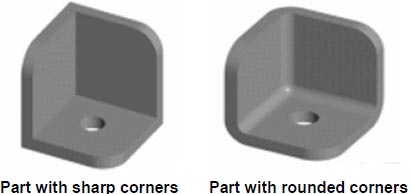
4) Parts with draft angles. The draft angles are must in plastics
products. The draft angle to be provided in the direction of ejection. The draft
angles can be half degree to one and half degree according to product
design requirement and plastic material to be use.
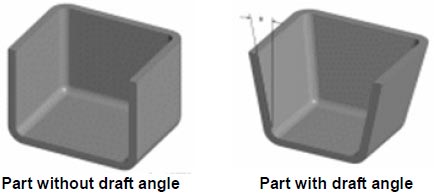 5)
Parts with ribs. The ribs can help to reduce wall thickness and confirm
application as it is. The ribs will eliminate warpage, sink mark etc. The ribs
design is also important to control weight of the component.
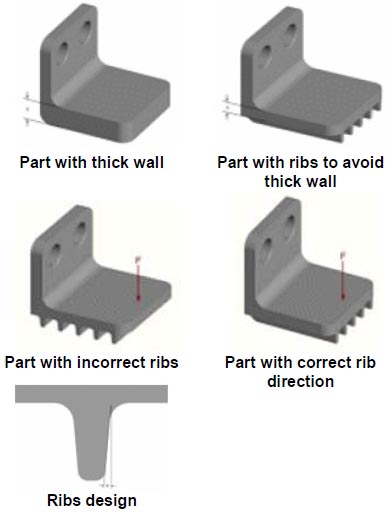 |