Designing And Manufacturing Of Molds For
Medical Components
6) Part design with boss
Sometime boss is required for clamping of two components with screw or pin. The
boss cannot be eliminating form the product design but the boss design has
different design possibility.
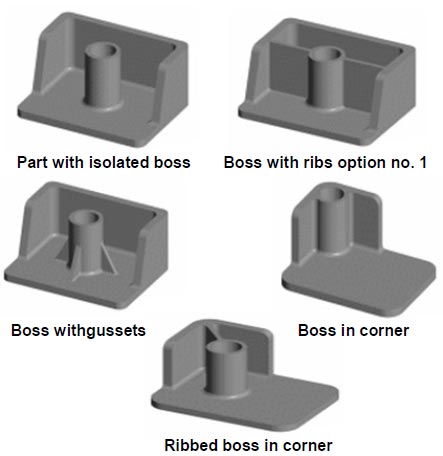
SELECTION OF STEEL MATERIAL FOR MEDICAL COMPONENTS
Selection of steel is very much important in medical plastics because the
product should be produce in corrosion free with highly polished mold surface.
The some of the recommendation+ of steel selection is as under.
1) Plastic materials like PET, Polyimide, PC, ABS, PEEK, PU, PMMA
• 1.2344,SKD61, H13 for better hardness and toughness
• 1.2083, AISI420 having 13% chromium for good polishing
• 718M high nickel alloy for corrosion resistance
• D53 (D2 supreme) for PC and PEEK material
2) Plastic materials like PP,PE,PS,PBT
• 8407 supreme for excellent toughness, high purity and fine structure
• S136, 1.2083 pre hardened steel for corrosion resistance
• 618,P20,1.2738,1.2711 for good wear resistance
3) Plastic materials like PVC,PA
• 718M nickel alloy ( 17-21% chromium, 50-55% nickel, 32-40 HRC)
• 1.2316 ( 15-17% chromium, 40-46 HRC)
SURFACE TREATMENT OF MOLD SURFACES
1) Hard chrome plating can be used for PP,PE,PS and ABS. We can get 72HRC
surface hardness.
2) Electroless nickel plating can be used for PVC,PC,PMMA and Polyamide. We can
get 50HRC hardness.
3) Titanium nitride plating can be used for glass filled material and PVC. We
can get hardness up to 90 HRC. It has good abrasive resistance, corrosion
resistance and excellent wear resistance.
METHODS OF PRODUCT DEVELOPMENTS
The product development technology improved a lot in last 10 years of period.
The product developed in past days with concept design sketch, then detail
drawing. With detail drawing model makers were making model from wood, plaster
of paris and acrylic sheets. This kind of proto type was time consuming and
without perfection. The modification in proto type was also difficult as
especially in intricate parts.
Then the product development was improved with 3D model in concept design. The
proto type was made with hand molds, jigs, fixture or cnc machining. This was
again time consuming and difficult in machining of intricate parts. This was
costly and disturbing production activity of tool room.
Now days it is very easy to develop product proto type without limitations. The
3D model of concept design is required. Then additive manufacturing processes
like SLS, SLA, FDM, 3D printing can be use for proto type model. This has only
one disadvantage of higher cost but development is possible in minimum time with
accuracy. The proto type can also use in application and confirm the function.
The plastic material of proto type is nylon, ABS, PC, epoxy resin and other
rubber based materials.
The proto type machines can be use for various applications and also for
marketing of product.
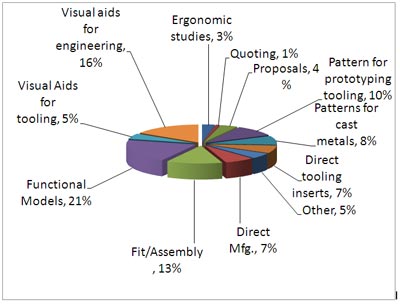
Some of the examples of product development with additive manufacturing.
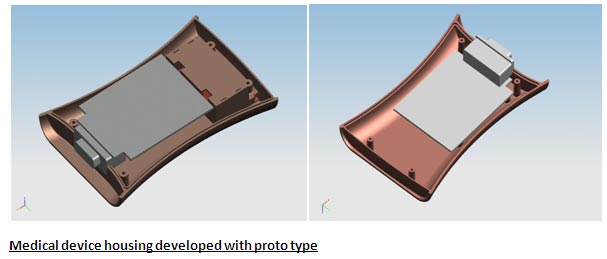
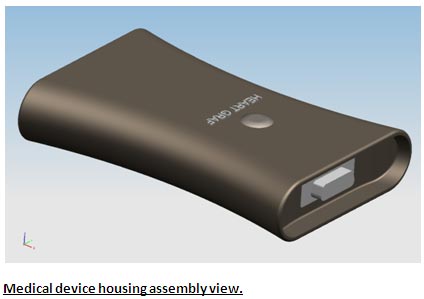
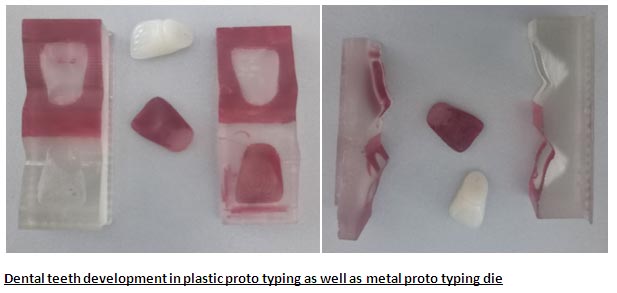
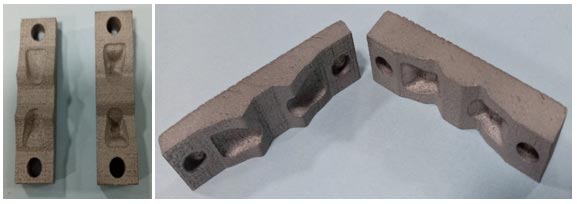
. |