High Volume Manufacture Of Thinwall
Medical Device Components
With Liquid Crystal Polymer Thermoplastics
(Courtesy : Celanese Chemicals The Chemistry Inside
InnovationTM)
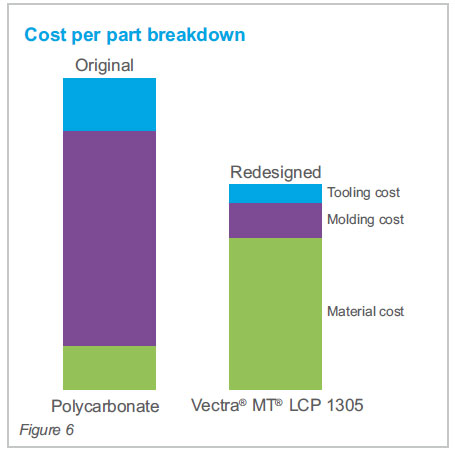
Customer value delivered
This collaborate approach to material
selection resulted in up to 50% per part cost savings
versus the incumbent Polycarbonate material. Savings
were realized through greater productivity with
shorter cycle times and increased multi-cavity tool
(4x versus original). Lastly, the simplified design
has allowed for increased flexibility for other
components.
Celanese solution & capabilities
Our Broad portfolio of Vectra® MT® LCP
includes glass-filled, mineral-filled, higher-flow,
tribologically modified (PTFE), and appearance grades
– suitable for a variety of uses in medical device
applications. There are also countless opportunities
for modified grades that provide extraordinary easy
flow and low warpage – ideal for highly complex
designs and for optimizing material use. This
functionality does not come at the cost of Medical
compliance, since all Vectra® MT® LCP grades are
supported by the Celanese MT® Polymer Service Package
including biocompatibility data to support regulatory
filings and to reduction of risk through change
notification, heightened quality procedures and
long-term supply agreements.
When working with the Celanese MT®
line of products, our Part Design & Processing team
includes industry-leading computeraided engineering
LCP design capabilities to allow conceptualization of
new part designs before tool production.
Summary
In summary, LCP resins are different
but not difficult. Once their polymer characteristics
are understood, they can be put to good use in pushing
the envelope with advanced designs, part to part
tolerance repeatability, and high volume productivity
in the tens of millions of units … all with the right
design, tooling and processing.
To assist with product development
from material selection to production, Celanese has a
dedicated technical team specializing in medical
applications to work with OEMs, (bio-) pharma
companies, molders, design houses, engineering firms
and CMOs/CDMOs.
Technical services include a world
class tribology lab to help with generating custom
test friction and wear data for optimum material
pairings in the medical device. This is in addition to
our standard CAE support for structural and mold
filling analysis and Field Tech Service support for
prototype to production mold trials. Selecting the
most appropriate medical grade (plastic?) materials
for complex electro-mechanical drug delivery devices
early in the project can facilitate a successful
launch and decrease risk of failure!. |