High Volume Manufacture Of Thinwall
Medical Device Components
With Liquid Crystal Polymer Thermoplastics
(Courtesy : Celanese Chemicals The Chemistry Inside
InnovationTM)
LCP exhibits a melting range rather
than a sharp melt point. The typical cure time is a
few seconds, with injection molding cycle time range
of ~5 to ~15 seconds for small part molding (depending
on # of cavities)
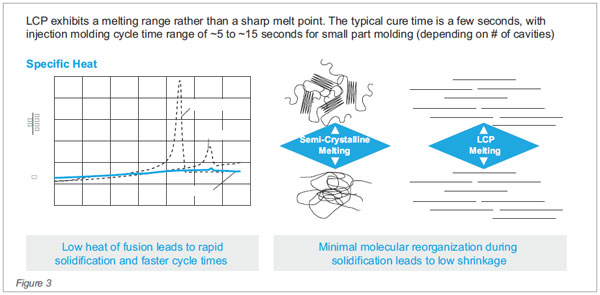
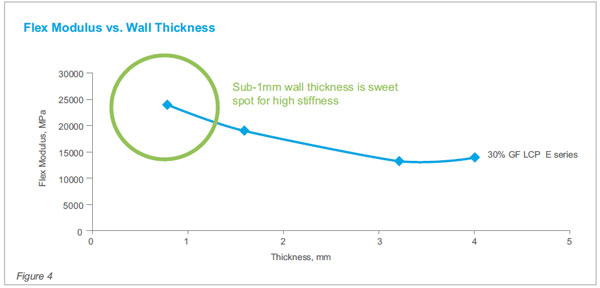
• Individual analytical tests per lot / delivery
(purity control) where appropriate
• Expanded certificate of inspection
• Change management aligned with GMP principles
• Support in Regulatory Approval
C. Design benefits from the use of LCP
Medical designers are looking for advanced and proven
polymer solutions to pack more technology into tighter
and lighter spaces for patient utility, comfort and
concealment. LCPs are valuable for wearable, portable
injector designs, diagnostic devices, injector pen
internals, surgical staple cartridges, surgical
instruments,
and microneedle arrays.
Vectra® LCP polymers are a natural fit for pushing the
envelope on thin wall designs to free up more internal
space without sacrificing product strength, stiffness,
and dimensional control. LCP resins increase in
strength & stiffness with thin wall designs due to
their unique rod-like molecular orientation. It’s a
paradigm shift in thinking, since thinner wall design
drives the final material properties to their
performance capable levels. Sub-1mm thickness wall
sections are the sweet spot for optimum mechanical
properties.
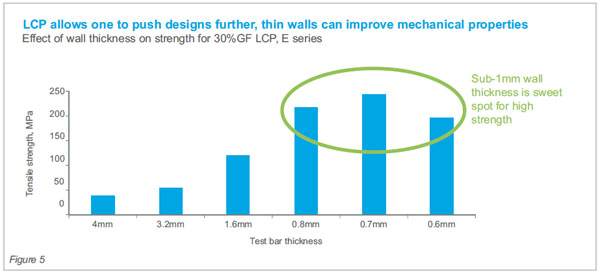
High stiffness and strength make LCP a candidate for
stainless steel or other specialty metal replacement,
where metal may be over-engineered for the
application. VLCP resins are available in a variety of
resin types and fillers for fine tuning strength,
shrinkage and tribology (wear & friction) properties.
See Fig 4 & 5 for how key mechanicals such as modulus
(stiffness) and tensile strength change as a function
of molded wall thickness.
Vectra LCP compounds are formulated in a variety of
polymer, reinforcement and additive compositions for
optimal mechanical, dimensional, thermal and
tribological properties.
Due to LCP extreme shear flow behavior, complex thin
wall designs that can’t be filled with other resins
can be filled with LCP and high micro-replication of
mold surface achieved, one reason why LCP is useful
for micro molded parts. Thin wall design enables fast
cycle times for higher productivity & reduced material
use & thus cost economy, important for single/limited
use products. Minimal molecular reorganization during
solidification not only leads to faster cycle times
but to low shrinkage for high precision, tighter
tolerance parts.
One caution with LCP is its lower weld-line strength
vs other composite resins like PPS so designs need to
be reviewed for weld-line locations. Butt welds should
be avoided as strength can be compromised as much as
90%. Gradually merging weld-lines are recommended. If
necessary, designers should relocate weldlines away
from high stress, critical areas or redesign those
areas for less stress in use.
D. Case study: Vectra® MT® LCP 1305 Lowers Cost Per
Part And Enables Improved Design For Wearable/On-Body
Injector Chassis
Customer challenge
Our OEM drug delivery customer had designed a wearable
injector that allowed patients to manage their
diabetes with an effective low maintenance treatment
approach. The designers were searching for material
solutions that optimized functionality while managing
overall device costs; especially critical since
components of the device were disposable.
The specific requirements for a lightweight,
cost-efficient wearable device called for excellent
mechanical performance including dimensional
stability, high stiffness and tight part tolerances
for the internal chassis. From previous experience we
were confident that such properties would increase
production efficiency by allowing for higher cavity
molds or shorter cycle times. Additionally, materials
that could allow for space savings inside the device
housing would provide opportunities to add
connectivity features or other electronics, and
generally increase design flexibility.
Our Field Development Engineers and Product
Specialists worked with the customer to replace a
Polycarbonate device chassis with a higher performing,
smaller component produced with one of Celanese
Medical’s medically compliant Liquid Crystal Polymer
grades.
After careful thought and collaboration, Vectra® MT®
LCP 1305 was selected. This is a 15% glass-reinforced,
higher-flow grade of LCP, enabling medical device
designers to develop a thinnerwalled, reducedweight
chassis and accelerate cycle times.
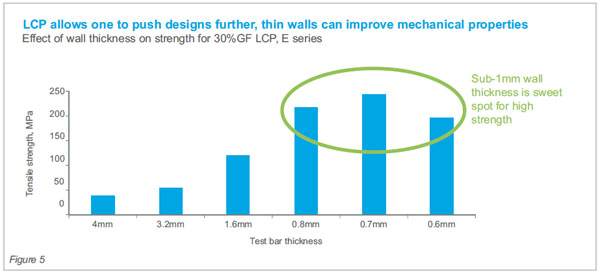 |