Emerging Trends In Medical Plastics
Over filling of pharma API is
a major cost especially in case of potent drugs. The
conventional ampoule/vial needs 18-23% over filling to
ensure accurate filling and dosing.
-
However, in case of PFS, this
overfilling drops down to as low as 2-3% thus saving
significant raw material cost to the manufacturer This is
observed more in case of biologics and potent drugs in
which the cost of API forms the major cost of raw material
used in the formulation.
-
PFS being a single closed
unit, is self sufficient and avoids additional medical
waste unlike in ampoule/vial which needs a disposable
syringe/ needle as an additional unit.
-
This makes it possibleto cut
down the waste formulation commonly called as left over
in the container. This reducing the medical waste.
-
Being single dose, ready to
use formulations, PFS makes it easier to use for a health
care practitioner or the patient in case of self
medication. Hence it has become a preferred choice due to
ease of administration and convenience. This also helps in
easy storage and disposal :
-
PFS being packed at the
manufacturer under sterile conditions and inspections,
least contamination issues are observed. Cross
contamination is also avoided being a single closed unit.
This ensures prolonged sterility of the formulation until
it is unpacked for administration.
-
While breaking the ampoule,
the glass flakes may go inside the container and thus not
only contaminate the formulation but these sharp edges are
also reasonably hazardous.
-
In case of emergency
situations in hospitals or mobile medical vehicles, PFS
serves as life saving delivery systems due to minimum
steps involved in administration of the drug as compare
with conventional delivery system which is time consuming.
-
Needle phobia is a major fear
in the western world especially with women, children and
geriatrics. PFS incorporates an almost hidden cannula thus
avoiding the visibility of needle to the patient
-
Color coding and individual
labeling on the PFS ensure minimum human administration
errors seen in case of multiple injection treatment and
emergency situations.
-
Different strength of same
drugs are also color coding either at the barrel label or
with different colored plunger rods.
-
Every year over 3 million
needle stick injuries take place globally. In case of PFS,
these needle stick injuries are avoided as it allows a
very natural handling and minimum time to fiddle with the
syringe. This has a huge impact on preventing cross
infections with HBC, HCV and HIV in public hospitals.
-
Some multi dose delivery
systems or storage containers like vials contain
preservatives like Thimerosal as in case of Vaccines. PFS
being single dose, avoids such unwanted ingredients in the
formulation.
-
Due to being a single
container for storage and delivery as well, PFS ensures
homogeneity within the formulation and hence a guaranteed
dosage is administered as per the expectation from the
label.
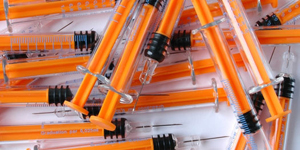
Some case studies in the
past have shown the benefits of using PFS over
conventional ampoule/vials. These are:
-
In 1998, a study by a group in
France demonstrated that using PFS over ampoule/vial saves
42% of administration time and justifies the additional
cost of PFS
-
In 2000, a study by a group in
Canada demonstrated that using PFS over ampoule/vial saves
25% of administration time
-
In 2010, a study at John
Hopkins, USA demonstrated that using PFS over ampoule/vial
saves over 70% of administration time in case of vaccines
and over a dollar per dose
-
A group in the Royal United
Hospital UK, studied the cost effectiveness of PFS
Thiopental against conventional delivery system. Most
preferred drug in emergency obstetric anesthesia by 93% UK
anesthetists. Of these 83% reconstitute it daily ensuring
safety at the cost of increased wastage and expense. With
PFS, shelf life increases to 90 days, and anannual cost
saving of over 60% in spite of being 1.8 times more
expensive than conventional formulation The above benefits
look very lucrative but there are a lot of challenges
involved in technically manufacturing a PFS. These
challenges increase with the number of components involved
in creating a single unit.Basically there are 5-6
components involved in a single unit of PFS which again
depends on the material of construction of the barrel of a
syringe, viz:
- Luer Tip / Needle Shield
- Luer Lock / Cannula
- Barrel
- Rubber Plunger
- Plunger Rod
- Flange
- Thumb pad
-
Various factors affect the
design and synchronization of these components which
together as a single unit make the PFS function. Some of
these factors include:
- Different Kind of patients
would have a different comfort level depending on
the disease, age group, strength etc.
- User could be a patient (selfmedication),
healthcare professional or the doctor himself
- Site of injection also influences the design and
hence every different site needs to be customized
- Drug Viscosity, more the viscosity, stiffer
plunger rod, and larger flange and thumb pad
- Needle Shield design size, surface texture,
material, grip, color, chemical properties, thickness
- Barrel design Glass or Polymer, shape, grip,
size, diameter, clearness, friability, strength,
curvatures, surface texture, roll-ability
- Plunger Rod design material, color, stiffness,
structure, size, thickness, motion, stability
- Flange design shape, size, grip, stiffness,
material, grooved
- Label design visibility, font size, color,
material, transparency
- Thumb pad design shape, size, surface slippery,
strength, stability, edges
- Packaging ease of pick up, unit size, handling
Its very important for all these components to function is
reasonable synchronization. Even during the design stage,
synchronization is of utmost importance. This is best
achieved when all the components are made under one roof
hence giving the best quality standards and control
uniform to each component. This also ensures zero
dependency on an outside vendor thus significantly
affecting the cost of the product.
Page
1 :
2 :
3 |