Inorganic Fillers
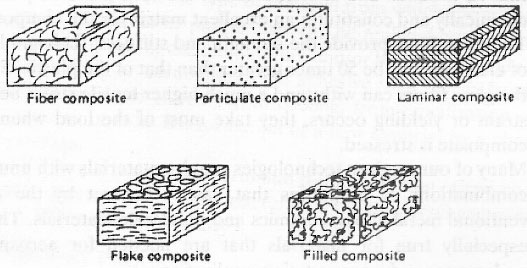
-
Oxides - Glass
(fibers, spheres, hollow spheres, and flakes), MgO,
SiO2, Al2O3, and ZnO
-
Hydroxides - Al
(OH) 3 and Mg (OH) 2
-
Salts - CaCO3,
BaSO4, CaSO4, phosphates, and hydrotalcite
-
Silicates - Talc,
mica, kaolin, wollastonite, montmorillonite,
feldspar, and asbestos
-
Metals - Boron
and steel
Organic Fillers
-
Carbon, graphite
- Carbon fibers, graphite fibers and flakes, carbon
nanotubes, and carbon black
-
Natural polymers
- Cellulose fibers, wood flour and fibers, flax,
cotton, sisal, and starch
-
Synthetic polymers
- Polyamide, polyester, aramid, and polyvinyl
alcohol fibers
Fillers are employed
to obtain any or combination of the following effects:
-
Lower Cost
-
Improve rigidity,
stiffness or hardness
-
Modify rheological
properties (flow, thixotropy)
-
Modify appearance
(opacity, color, texture)
-
Regulate shrinkage and
thermal expansion
-
To improve heat
resistance
-
To improve the
electrical characteristics
-
Increase strength and
reduce creep
-
Aid processability
(lubrication, flow, mixing, dispersion etc.)
-
Alter density and bulk
Radiopaque
additives Devices like
catheters, guide tubes, surgical tools, dental
products, stents and balloons that are used inside the
body, in many cases, need to be opaque to fluoroscopy
or X-rays so that the surgeons are able to see the
devices as it is guided through or placed in the body
.Most plastics are transparent to X-rays and require
additives that are radiopaque. The most common
radiopaque additives are given below which render the
plastic visible under X-rays and work as well as lead
without any of the toxic side effects or disposal
concerns.
-
Barium sulphate
is the most commonly used radiopaque additive with a
particle size ranging from 0.5 to 2.0 µm. It can be
incorporated into a polymer at high loading level
(approx 60%) without significant loss in physical
properties of the polymer. It is also resistance to
acids and alkalies and has very good weathering
resistance.
-
Bismuth compounds
are also used as radiopaque additives. They are
denser than barium sulphate. The same level of
radiopacity can be obtained with lower loading
levels of the bismuth compounds compared to barium
sulphate.
-
Tungsten has a
specific gravity of 19, twice that of bismuth
compounds. Low loading levels of tungsten are
required to obtain the same level of radiopacity
while still maintaining good physical and mechanical
properties. Tungsten is used in thin walled
applications (0.1-0.2 mm wall thickness)
-
Tantalum has been
used as a radiopaque additive on bone cements.
Indian and International Survey
Customized polymers filled with required amount of
barium sulphate are being manufactured out of India.
There are many industries manufacturing barium
sulphate in India but very few manufacturing barium
sulphate filled thermoplastic polymers. So development
of these types of polymers will help to develop a new
area of business in Indian market. These types of
customized polymers are already being used in the
medical devices and so usage of them will be in
demand.
Plastics in medical devices
-
20% of all plastics
(Nylons, polyesters, PC , polyurethanes, Acrylics,
Acetals) Surgicals instruments, balloons, blood
set components, blood bowls, blood oxygenators,
syringes, moving parts and components, catheters.
-
10% of all plastics (Polyimides,
Polyetherimides,, Polyetherether ketones,
polyphenylene sulfide, Flouropolymers, Liquid
crystalline polymers, Biopolymers, Thermoset and
adhesives) Surgical instruments, Surgical trays,
Syringes, Implants, Dental implants, Bone implants,
Moving part and components, High precision parts,
Electronic components.
-
70% of all plastics (PE,PP,PS,PVC)
Tubing, films, packaging, connectors, labware,
IVbags, catheters, facemasks, drug delivery
components, housings, membranes, sutures, syringes.
Advantages of using
plastics in medical device
-
Design flexibility
-
Miniaturization of
components
-
Light weight
-
Electrical insulation
and conductivity
-
Thermal insulation and
thermal conductivity
-
Color
-
Ability to be metalized
-
Transparency
-
Water resistance
-
Chemical and lipid
resistance
-
No allergic-Fungus
resistance
-
Mass produced and low
cost to produce/economies of scale
-
Design freedom
-
Ease of processing and
processing methods, processibility
-
Fillers and additives to
tailor properties Bondability
-
Sterilization
-
Glass and metal
replacement
|