Invited Speakers & Panel
Experts : Presentation Abstracts
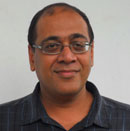 |
Mr. T.S. Kumaravel
(Founder Chairman, GLR Laboratories Pvt. Ltd.,
Chennai)
“How to fulfill biocompatibility in today’s rapidly
changing regulatory and scientific scenario?”
It is the management
responsibility to assure the safety of medical devices
that they placed in the market. One of the safety
requirements is to fulfill the biocompatibility of the
medical device.
Biocompatibility
testing provided confidence to the manufacturer,
regulators and the patients that the device is safe
for the intended use.
General guidance for
biocompatibility testing is provided by ISO10993, Part
1. The other parts of ISO 10993, Parts 2-20 give
guidance on how to perform these tests. There are also
other guidance that are device specific. These device
specific guidance
are issued by ISO, regulatory bodies and sometimes
scientific committees can issue recommendations.
Biocompatibility
testing and guidance came into use in mid 1990s, when
ISO started developing guidelines. Initially the
regulators and notified bodies looked at
biocompatibility as a mere box ticking exercise. At
that time, certificate that biocompatibility was
fulfilled was considered sufficient. With further
developments and revisions in ISO standards, and
further experiences in biocompatibility testing over
the last 10 years, the expectation from
biocompatibility testing has massively increased. The
regulators and the notified bodies have started
looking at the biocompatibility reports in greater
details for scientific and regulatory fulfilments.
They are employing biocompatibility experts to review
the files submitted to them for CE marking or 510K/PMA.
Under these
circumstances, it is important for the manufacturers
to understand these changing requirements and prepare
their biocompatibility files accordingly. There is
also more emphasis on literature review and risk
management approached to fulfil
biocompatibility requirement, without the need for
unnecessary animal testing.
In this talk, I will
briefly introduce you to these changing regulatory
requirements in biocompatibility testing. |
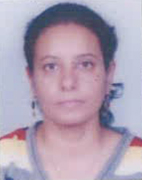 |
Dr. Manasi Nath,
(Technical Application Engineer,
Kraton Polymers International Ltd. Mumbai)
“Novel Styrenic Block
Copolymers and Polyisoprene Rubber for Medical
Devices.”
Styrenic Block
Copolymers (SBCs) and polyisoprene rubber are suitable
for a variety of applications. This paper describes
Kraton® polymers, especially Kraton Enhanced Rubber
Segment SEBS (Kraton®ERS SEBS) in transparent medical
applications. Due to their cleanness, softness, good
processability and excellent compatibility with
polypropylene, Kraton ERS SEBS polymers have been
widely used, as a toughness modifier for
polypropylene, in transparent medical application such
as IV bag ilms, medical tubing and consumer goods
application such as containers, etc.
Cariflex®Polyisoprene Products are designed to replace
natural rubber for producing medical products ranging
from surgical gloves and tube connectors to IV bag and
medical stoppers, balloon catheters, needle shields,
dental dams and cohesive bandages. |
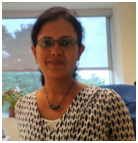 |
Dr. Pallavi Kulkarni
(Technical Manager
Lubrizol Life Sciences, Lubrizol Advanced Materials,
USA)
Thermoplastics Polyurethanes: Enabling Innovative
Competitive Technologies through Advanced Materials
Thermoplastic Polyurethanes (TPUs) are a class of
polymers with unique physicochemical properties. They
are inherently strong like thermoplastics yet flexible
like elastomers, making them the most versatile class
of polymers. TPUs are composed of soft and hard
building blocks and the phase segregated morphology of
these building blocks imparts physical properties that
cover the entire range of polymers from soft, flexible
elastomers to rigid engineered polymers and everything
in between. Additionally, the soft and hard blocks can
be chemically chosen such that they are biocompatible
and biostable, suitable for medical applications.
Medical Device industry has grown exponentially in the
last decade with an evolving regulatory landscape.
Device design engineers are constantly looking to
create the next-generation device with advanced
polymers and materials that offer an edge over
existing materials. The versatility and tailor ability
of thermoplastic polyurethanes has become an essential
tool in the design engineer’s toolbox. TPUs have
successfully replaced PVC for certain device
applications where regulations prohibit the use of
plasticizers. In some other instances, TPUs are being
used instead of silicones in next generation devices,
thereby providing a competitive edge in the
marketplace.
Lubrizol’s medical grade TPU offer a wide range of
chemistries to choose from depending on the
application. Ease of process ability is key for
efficient manufacturing, Lubrizol’s TPUs can be
processed by standard methods such as extrusion,
injection molding, and solvent casting. With the
addition of Vesta, Lubrizol has gained additional
capabilities more towards device manufacturing and
assembly. Lubrizol is no longer just a resin supplier;
it is a complete Device Solution provider. |
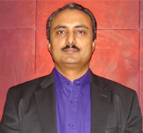 |
Mr. Shinto Joseph
(Director,
LDRA Technology Pvt. Ltd., Bangalore.)
"Process oriented
approach for building safer and secure medical
devices"
For
medical device developers, increased government
scrutiny and new international standards create a
compliance burden that challenges time-to-market goals
and threatens to explode development costs. Along with
Safety, now Security is also a serious concern for all
and without global safety certifications, today our
innovations cannot reach global markets. We would
discuss international safety standards like IEC 62304
and secure software development approaches that could
help in accelerating your go to market strategy, while
keeping the costs under check. |
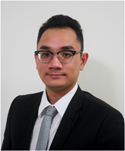 |
Mr. Derrick Chan
(Head, Regional Segment Healthcare Polymer Solutions,
Asia Pacific, Clariant (Singapore) Pte. Ltd.)
“Coloration &
Modification of Medical Plastics – Managing Risk & New
Opportunities.”
Designers and manufacturers of medical devices and
pharmaceutical packaging invest significant time and
money in meeting performance and regulatory standards
to fulfil the increasingly stringent demands of these
global markets. Materials that can help minimize the
risks and costs of non-compliance in a product’s
development and lifecycle are vital to this process.
Clariant’s package of dedicated service and expertise,
product reliability and innovative material
performance gives the industry the confidence it needs
to address risk potential. |
Page
1 :
2 :
3 :
4 :
5 :
6 :
7 :
8 :
9 :
10 :
11 :
12 :
13 :
14 :
15 :
16 :
17
|