Medical Polymers In India: Technological Developments And
Growth Pattern
Facilitates Diagnosis And Treatment
.
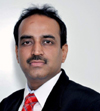
.Mr. Govind Khetan
Vice President (Sales & Marketing) India
Kraton Polymers International Ltd., New Delhi |
Mr.
Govind Khetan holds a Bachelor’s degree in Polymer
Technology from University of Pune. He is presently
the Vice President and Country Head for Kraton
Polymers India. His previous professional assignments
were with reputed Multinational and Indian
corporations – DSM Engineering Plastics, Indofil and
Gharda Chemicals. He can be reached on
govind.khetan@kraton.com |
The growth of consumption for
medical polymers in India.
We believe that the medium to
long-term prospects for the Indian Healthcare Sector are
very good as growing levels of lifestylerelated chronic
diseases and higher life expectancy are driving demand.
Over the years, India has emerged as preferred destination
for medical tourism due to the superior quality of
healthcare being offered at competitive prices. Today,
India hosts about 150,000 medical tourists every year. The
Indian Healthcare Sector has been estimated at around US
$75 billion, growing at 12-15% CAGR, employing nine (9)
million people.
Innovative solutions based on
polymer technology play a significant role in facilitating
diagnosis and treatment via incorporation in medical
devices, implants and disposables. Modern healthcare
demands an increasingly higher proportion of polymers in
syringes, IV fluid bottles and bags, personnel hygiene and
sanitary products. Key drivers for the use of medical
polymers in healthcare are safety, lightweight,
functionality and inertness, among others.
The specific product areas
where polymers being supplied by the company have
substituted conventional materials for medical
applications.
We develop and produce
advanced, engineered synthetic elastomers designed to meet
the specific requirements of medical product
manufacturers. Kraton™ polymers and polymer-modified
systems perform like polyvinyl chloride (PVC) but are
formulated without PVC, phthalates, plasticizers and
volatile organic compounds (VOCs). As a result, the Kraton
materials do not have the health concerns associated with
plasticizers and are environmentally sound as well as
recyclable. Our styrene block copolymers (SBCs) are widely
recognized for their ease of processing and combination of
physical properties including clarity, flexibility,
resilience, strength and durability. The materials exhibit
outstanding costperformance benefits for producing tough,
transparent, medical tubing and IV bags, as well as a
broad range of single - use, nonwoven fabrics and wound
dressings.
Next generation Kraton
enhanced rubber segment (ERS) styrene-ethylene/butylenestyrenes
(SEBS) are characterized by even greater handling and
performance properties. The polymers are highly compatible
with polypropylene (PP) to form extrudable and moldable
compounds with improved flow without plasticizers. ERS
SEBS can withstand most hospital sterilization methods and
are well suited for producing high-clarity medical bags,
tubes and flexible films.
Additionally, our Cariflex™
polyisoprene products are manufactured using a simple but
highly efficient polymerization process developed by
Kraton. Cariflex™ is proving to be a superior alternative
to natural rubber because it is free from naturally
occurring rubber proteins that can trigger Type I allergic
reactions. The high-strength material it produces ensures
the production of strong but comfortable surgical gloves,
leak-resistant medical stoppers and highelongation,
resilient physiotherapy and tourniquet bands.
Effect of Improving
Regulations on the global medical device industry. The
regulations and compliance criteria met by Polymers
Supplied by The Company.
We are not directly impacted
by changes made in regulations for medical devices because
our polymers are only a part of the compound used in the
medical device, and testing is performed on the device
itself. However, our medical customers do ask about the
United States Pharmacopoeia (USP) status of our polymers,
and we are pleased to tell them that most of our polymers
meet the requirements of USP Class VI and, additionally,
many are now tested for cytotoxicity and hemolysis.
Polymers for Packaging
Applications.
Kraton polymers are used as a
PVC alternative for medical packaging. We develop and
produce advanced, engineered synthetic elastomers designed
to meet the specific requirements of medical product
manufacturers.
Kraton G SEBS and SEPS
polymers are the strongest, the most highly dilutive, and
the most compatible with polyolefins and mineral oils of
all the styrenic thermoplastic block copolymers. Kraton G
polymers are second-generation SBCs with a hydrogenated
midblock of SEBS or styrene-ethylene/propylene-styrene (SEPS).
They are intended for use where UV resistance, high
service temperature, and processing stability are
essential. These Kraton G polymers are used for a variety
of medical packaging.
New developments in the
polymers supplied by the company.
Kraton is an innovation-led
growth organization. Identifying, assessing and
understanding the needs of the medical markets and the
customers we serve continue to be a primary driver for our
business strategy. We are constantly working both up and
down the medical market value chains to identify and
create new performance features and benefits needed in our
next generation products. Our capabilities allow for the
ability to work with our various customers in the medical
industry to provide
tailored polymer and compound structures targeting
value-added and differentiated solutions. Many of our
traditional Kraton G polymers and compounds are used
across the medical market space as viable alternatives to
PVC in a variety of medical applications. Kraton G ERS
polymers represents an innovation line of materials that
were created to provide improved purity and low
extractable performance, while promoting enhanced
durability, impact resistance, elasticity, flexibility,
clarity and
compatibility characteristics in medical applications. As
mentioned earlier, our Cariflex™ polyisoprene products
were designed to replace natural rubber for molding
medical products ranging from surgical gloves and tube
connectors to IV bag and medical stoppers, balloon
catheters, needle shields, dental dams and cohesive
bandages. Available in both solid and latex forms,
Cariflex products are manufactured using a Kratondeveloped
advanced polymerization process that eliminates
impurities.Cariflex products are easy to process with the
same equipment and methods used for traditional natural
rubber, i.e. dip molding (IRL), compression and injection
molding as well as extrusion, among others. Like natural
rubber, our polyisoprene products exhibit high tensile
strength and tear resistance along with good elasticity
and durability. Medical products formed from Cariflex
latex materials have a soft feel, strength and reliable
protection.
Page
1 :
2 :
3 :
4 :
5 :
6 :
7 :
8 :
9 :
10 |